
大概有40K库存用英文怎么说
Inventory Management and Optimization
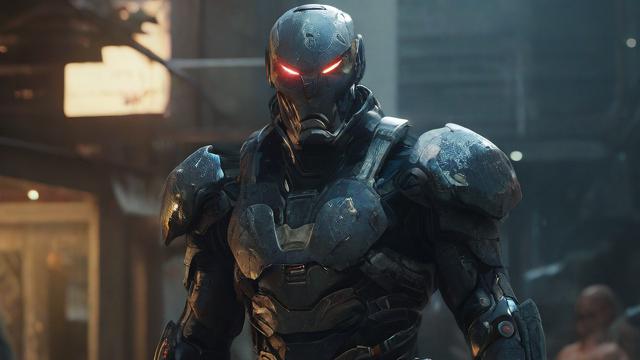
1. Current Inventory Situation
1.1 Inventory Overview
Currently, we have approximately 40K units in stock. This inventory level is a significant asset for our business operations, ensuring that we can meet customer demand promptly and maintain a stable supply chain. However, it also poses certain challenges in terms of storage, management, and financial implications.
1.2 Inventory Composition
The 40K inventory consists of various products, each with its own unique characteristics, demand patterns, and shelf life. To better understand and manage the inventory, we can categorize the products as follows:
Product Category | Quantity (units) | Percentage of Total Inventory | Key Characteristics |
Fastmoving Consumer Goods (FMCG) | 15,000 | 37.5% | High demand, short shelf life, frequent replenishment required |
Electronic Products | 8,000 | 20% | Moderate to high demand, longer shelf life but susceptible to technological obsolescence |
Mechanical Parts | 6,000 | 15% | Stable demand, long shelf life, but may require specific storage conditions |
Textiles and Apparel | 5,000 | 12.5% | Fashionoriented, seasonal demand variations, sensitive to storage environment |
Chemicals and Raw Materials | 4,000 | 10% | Used as inputs for production, bulky and may have storage hazards |
Others | 2,000 | 5% | Diverse range of products with varying demand and storage requirements |
1.3 Storage Considerations
Given the size and diversity of our inventory, efficient storage is crucial. We need to consider factors such as space utilization, accessibility, and environmental conditions. For example, FMCG products may require temperaturecontrolled areas to maintain their quality, while electronic products need to be stored in dry environments to prevent damage from moisture. Proper storage not only ensures the integrity of the inventory but also minimizes losses due to spoilage or damage.
2. Inventory Management Strategies
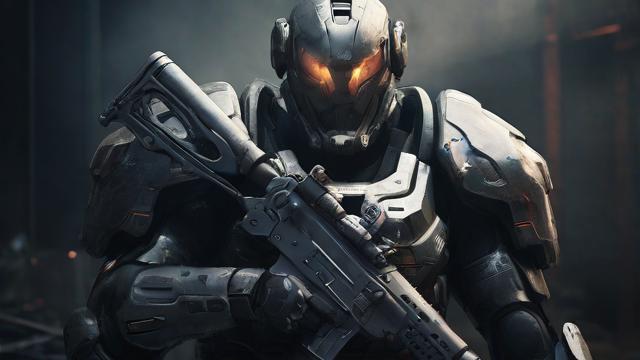
2.1 Demand Forecasting
Accurate demand forecasting is essential for effective inventory management. By analyzing historical sales data, market trends, and customer behavior, we can predict future demand for our products. This enables us to plan our inventory levels accordingly, avoiding overstocking or stockouts. For instance, if we anticipate a surge in demand for a particular product during a certain season or due to a marketing campaign, we can increase our inventory in advance to meet the expected demand. Conversely, if demand is expected to decline, we can reduce our inventory to avoid excess stock.
2.2 Inventory Turnover Rate
Monitoring the inventory turnover rate helps us assess how efficiently we are managing our inventory. The inventory turnover rate is calculated by dividing the cost of goods sold by the average inventory level. A higher turnover rate indicates that our inventory is selling quickly, which is generally desirable as it reduces holding costs and frees up cash for other investments. On the other hand, a low turnover rate may suggest overstocking or slowmoving products. For our current 40K inventory, we need to calculate the turnover rate for each product category and identify areas where improvements can be made. For example, if the FMCG category has a high turnover rate, we should ensure that we have sufficient stock to meet the demand without running out. If the chemicals and raw materials category has a low turnover rate, we may need to review our purchasing plans and supplier contracts.
2.3 Safety Stock Levels
Safety stock acts as a buffer against unexpected fluctuations in demand or supply chain disruptions. Determining the appropriate safety stock levels involves considering factors such as lead time variability, demand uncertainty, and the cost of stockouts. For our 40K inventory, we need to analyze the historical data and market conditions to set reasonable safety stock levels for each product. This will help us maintain a balance between avoiding stockouts and minimizing excess inventory. For example, for critical components used in production, we may need to maintain higher safety stock levels to ensure continuous production in case of supplier delays. For nonessential items, we can keep lower safety stock levels to reduce carrying costs.
3. Inventory Optimization Techniques
1 ABC Analysis
ABC analysis is a method of categorizing inventory based on its importance and value. It divides the inventory into three categories: A, B, and C. Category A items are highvalue products that account for a large percentage of the total inventory value but represent a small percentage of the total number of items. These items require close monitoring and tight control. Category B items have moderate value and quantity, while category C items are lowvalue products that make up a large portion of the total number of items but contribute relatively little to the total inventory value. By applying ABC analysis to our 40K inventory, we can prioritize our management efforts and resources. For example, we may focus more on optimizing the stocking levels and replenishment strategies for category A items to maximize their contribution to our profitability.
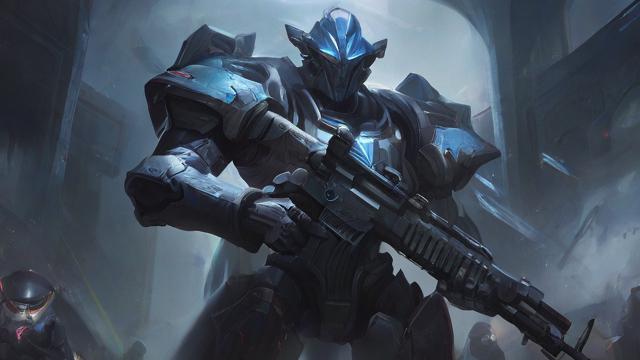
3.2 JustinTime (JIT) Inventory System
The JIT inventory system aims to minimize inventory levels by receiving and using materials and products just as they are needed in the production process. Implementing JIT requires close coordination with suppliers, efficient production scheduling, and reliable transportation. For our business, adopting JIT can reduce inventory holding costs and improve cash flow. However, it also increases the risk of stockouts if there are any disruptions in the supply chain. Therefore, before implementing JIT, we need to carefully evaluate our suppliers' reliability, production flexibility, and logistics capabilities. We may start by applying JIT to a few selected products or categories that are suitable for this approach and gradually expand its scope as we gain experience and confidence.
3.3 Inventory Replenishment Strategies
Choosing the right inventory replenishment strategy depends on various factors such as lead time, demand variability, and product characteristics. Some common replenishment strategies include:
Fixed Order Quantity (FOQ): In this strategy, a fixed quantity of inventory is ordered each time an order is placed, regardless of the current inventory level. It is suitable for products with relatively stable demand and predictable lead times.
Fixed Order Interval (FOI): With FOI, orders are placed at regular intervals, and the order quantity varies depending on the inventory level at the time of ordering. This strategy works well for products with high demand variability or when economies of scale can be achieved by ordering larger quantities less frequently.
Maximum Order Quantity (MOQ): MOQ sets a maximum limit on the quantity of inventory that can be ordered at one time. It is useful for controlling inventory costs and preventing overstocking, especially for bulky or expensive items.
Minimum Order Quantity (MOQ): Similar to MOQ, but it specifies the minimum quantity that must be ordered each time an order is placed. This ensures that the supplier can produce and deliver efficiently while still meeting our basic inventory requirements.
For our 40K inventory, we may use a combination of these strategies for different product categories. For example, we can use FOQ for fastmoving consumer goods to ensure timely replenishment and avoid stockouts, and FOI for electronic products where demand is more variable.
4. Inventory Cost Management
1 Holding Costs
Holding costs include expenses related to storing inventory, such as rent, utilities, insurance, and depreciation. For our 40K inventory, holding costs can be significant, especially for items that require special storage conditions or have long storage periods. To reduce holding costs, we can:
Optimize warehouse layout and space utilization to store more inventory in a smaller area.
Negotiate better rental terms or consider alternative storage options.
Implement inventory rotation policies to ensure that older inventory is used first and reduce the risk of obsolescence.
Evaluate the necessity of maintaining high safety stock levels for certain products and adjust them based on actual demand patterns.
2 Ordering Costs
Ordering costs encompass the expenses associated with placing an order, including administrative costs, transportation costs, and supplier charges. Minimizing ordering costs involves finding the optimal order quantity and frequency. By analyzing our demand patterns and supplier terms, we can determine the most costeffective way to place orders. For example, if ordering costs are high, we may consider consolidating orders with multiple suppliers or increasing the order quantity to take advantage of volume discounts.
4.3 Opportunity Costs
Opportunity costs refer to the potential benefits that are forgone by holding onto inventory instead of investing that capital elsewhere. For instance, if we have a large amount of capital tied up in inventory, we may miss out on other investment opportunities that could generate higher returns. To mitigate opportunity costs, we need to regularly review our inventory levels and financial performance and make informed decisions about whether to reduce inventory or reallocate funds to more profitable ventures.
FAQs
Q1: How can we effectively track and manage the perishability of FMCG products in our 40K inventory?
A1: To manage the perishability of FMCG products, we can implement a firstin, firstout (FIFO) inventory rotation system. This ensures that the oldest products are sold first before they reach their expiration date. We can also use inventory management software that provides alerts for products nearing their expiration dates so that we can take timely actions such as discounting or donating them if necessary. Additionally, proper storage conditions, such as maintaining the recommended temperature and humidity levels, are crucial to extend the shelf life of perishable items.
Q2: What are some ways to handle slowmoving or obsolete inventory in our 40K stock?
A2: For slowmoving or obsolete inventory, we have several options. First, we can try to liquidate them through special sales promotions, such as clearance sales or bundle offers. If the products are still in good condition but simply not selling due to lack of demand, we can consider donating them to charities or social welfare organizations. Another approach is to repurpose or rework the inventory if possible. For example, if we have old textiles that are no longer fashionable, we can convert them into cleaning rags or other useful items. If the products cannot be salvaged in any way, we may need to dispose of them properly while considering the environmental impact.
Q3: How can we improve communication and coordination with suppliers to optimize our inventory management?
A3: Improving communication and coordination with suppliers is vital for efficient inventory management. We can establish regular communication channels with our suppliers to share information about demand forecasts, production schedules, and potential supply chain disruptions. This allows both parties to plan ahead and make necessary adjustments. Collaborating with suppliers on inventory planning can also help us achieve better economies of scale. For example, we can work together to set up consignment inventory agreements where suppliers hold the inventory and only charge us when it is actually used or sold. This reduces our inventory holding costs and risks. Additionally, using shared technology platforms for realtime visibility into inventory levels and shipment statuses can enhance coordination and responsiveness.
作者:豆面本文地址:https://www.jerry.net.cn/articals/36218.html发布于 2025-03-01 11:23:48
文章转载或复制请以超链接形式并注明出处杰瑞科技发展有限公司